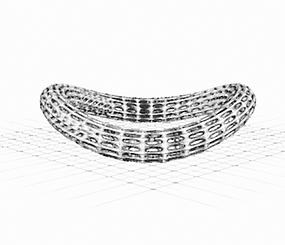
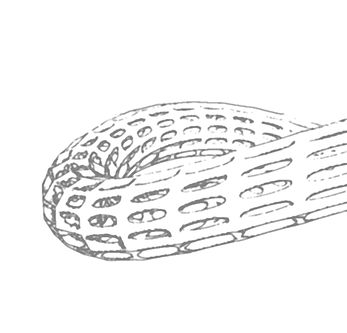

How MèRIDESIGNS Makes Jewellery With 3D Printing
Working with 3D printing gives me limitless creativity. I’m intrigued by the aesthetic possibilities of this fast-evolving technology that are essential to the way I craft jewellery. It allows me to create complex geometric shapes that would be very difficult to achieve by hand or using traditional manufacturing. This way of working also gives me the freedom to experiment with new ideas without wasting lots of materials.
​
Each MèRIDESIGNS piece begins with a hand drawn sketch which I then render in 3D modelling software to create digital prototypes for printing. Then I print a prototype to assess size, scale, proportion and to identify any potential design, assembly or finishing issues. When I’m satisfied with the results, it’s time for the final printing stage.
My Creative Process
My collections are built around different concepts that inspire me, including the complex geometry found in nature, and contemporary art and architecture. I’m always learning and evolving techniques and materials to keep my work fresh and innovative. Before starting a new jewellery collection, I do extensive research, studying shapes, materials and new techniques developing my own aesthetics.
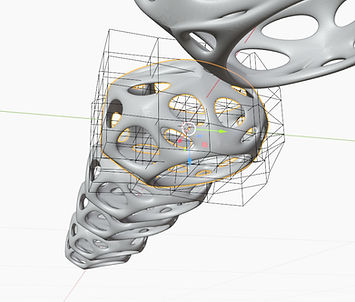
Digitally Sculpting
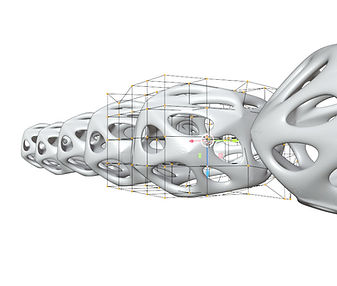
Parametric Rings
Sustainable Production Practices
All my pieces are digitally designed and hand-finished using materials including gold, silver, stainless steel and synthetic fibres. I’m often asked if 3D printing technology is a sustainable manufacturing process. What makes my work sustainable is a mix of the processes and only making jewellery to order.
The 3D process only uses the material it needs for the individual piece and produces minimal scrap waste, approximately 70-90% less than some traditional manufacturing methods. It also uses less energy and has a smaller carbon footprint.